FSW (Friction Stir Welding) cold plates
FSW (Friction Stir Welding) is used by Atherm for Cold Plates manufacturing.
From design implementing optimized thermal features according FSW know how, to serial production in our facility, Atherm is able to propose efficient FSW Cold Plates according to your specification.
Friction Stir Welding Cold Plates can easily replace Vacuum brazed, welded or Embedded tubes Cold Plates with many advantages.
Friction Stir Welding, How it works
Friction Stir Welding (FSW) is a solid-state welding process used to join two metal pieces without melting the metal. It was invented in 1991 by The Welding Institute (TWI) in Cambridge, UK. FSW is particularly useful for joining high-strength aerospace alloys and other materials that are difficult to weld using traditional welding techniques.
In FSW, a hard material rotating tool, typically tungsten carbide, is plunged into the two metal pieces to be joined. The tool is then moved along the joint line, generating frictional heat that softens the metal without melting it. The softened metal is stirred together by the rotating tool, forming a solid-state joint.
- The two sheets to be welded are placed into contact and firmly clamped.
- The rotating tool (400 to 3500 rpm) penetrates the material and then moves along the joint line (10 to 100 mm / s).
- The tool consists of a shoulder and a pin. The pin plunges into the material by heating until the shoulder comes into contact with the sheets.
- The pressure has to be sufficient so that the heat generated by friction between the shoulder and the sheets can soften the material without reaching the melting point.
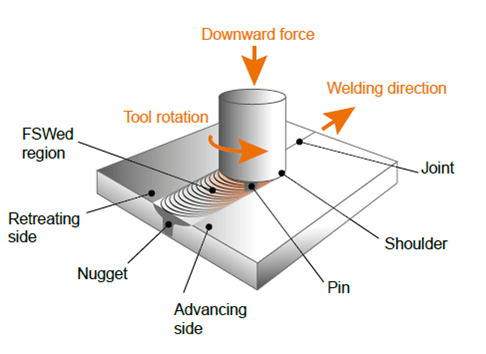
Friction Stir Welding Cold Plates Advantages
FSW has several advantages over traditional welding techniques for the manufacturing of Cold Plates. It produces joints with high strength and good fatigue properties, and it can be used to join dissimilar metals. FSW also produces a narrower heat-affected zone than traditional welding techniques, which reduces distortion and improves dimensional stability.
HIGH THERMAL PERFORMANCE
EASY PROCESS TUNING
LOW DEVELOPMENT COSTS
2 to 10 times less expensive than other existing process
HIGH REPEATABILITY AND RELIABILITY
MATURITY
NO POST HEAT TREATMENT
HIGHER RESISTANCE COMPARED TO BRAZED COLD PLATES
ALUMINIUM AND COPPER WELDING
FROM SMALL TO LARGE SERIES
From an aluminium block and a cover it is easy to manufacture a ready to use waterproof thermal management part.
Examples of FSW applications
FSW is widely used in the aerospace industry to join aluminum, titanium, and other high-strength alloys. It is also used in automotive, shipbuilding, and other industries that require high-strength, high-quality welds.
Thin liquid FSW cold plate
Total thickness: 3mm Welding process: lap welding of 3 1-mm aluminium sheets in one step.
Pressure resistance: 9 bars
Our Machines for Friction Stir Welding production
CUCN / MAZAK VC SMART 530 C / 3 axes / table : 1300x550 - courses X= 1050 Y= 530 Z= 510
CUCN / CHIRON FZ18 / 3 axes, palettisé / courses X= 630 Y= 400 Z= 400
CUCN / CHIRON FZ12 / 3 axes, palettisé / courses X= 550 Y= 300 Z= 280
CUCN / DMG 103 / 3 axes / courses X= 1 030 Y= 600 Z= 600
CUCN / DMG 635 / 3 axes / courses X= 635 Y= 500 Z= 400
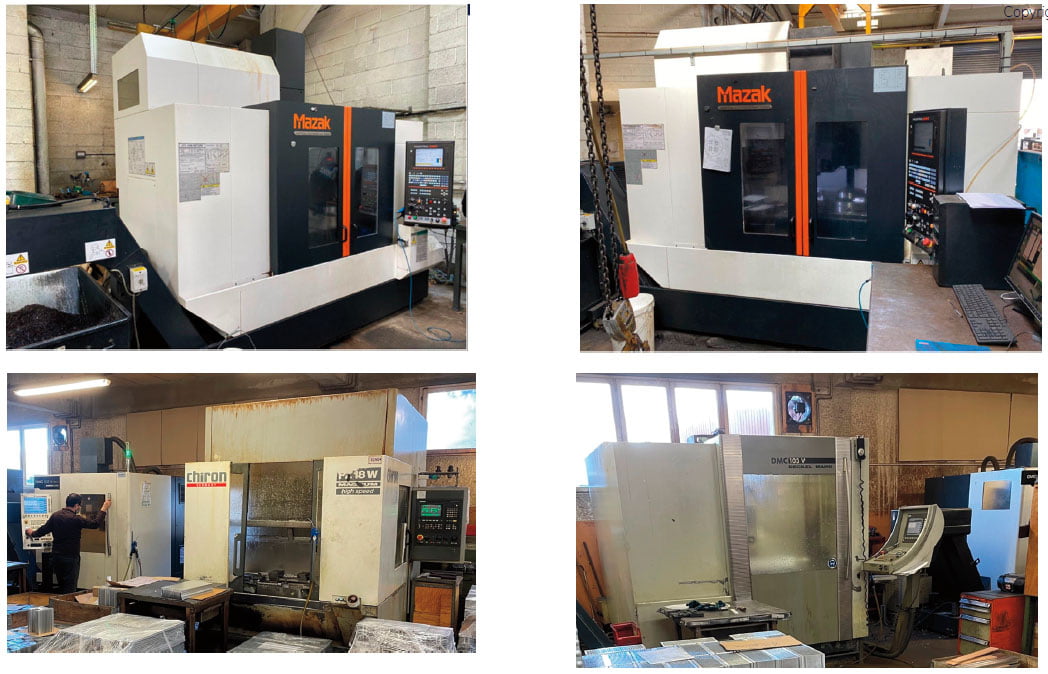